Le sfide del manifatturiero si affrontano con una strategia manutentiva che si avvalga di pratiche efficaci, tecnologie e know-how dei fornitori. Scopriamo come “rigenerare” garantisca impatti economici e ambientali notevoli.
Avere processi produttivi che siano più efficienti e che sappiano guardare ai temi della sostenibilità è importante per ogni impresa. A maggior ragione in un periodo come l’attuale in cui questioni quali i prezzi delle materie prime, dell’energia e il livello di un’inflazione crescente passano dall’essere delicati a cruciali.
Per poter progettare e applicare una politica interna che consenta di raggiungere obiettivi di efficientamento e di sostenibilità dei processi bisogna strutturare una strategia mirata che sia però, anche, strategia manutentiva.
Ne ha parlato al Congresso Aticelca 2022 Pierluigi Prete, key account manager and P&P industry leader di SKF Industrie.

Gli asset e il ciclo di vita delle macchine
La strategia manutentiva di un’azienda per essere efficace deve avvalersi di una serie di elementi «pratiche efficaci, tecnologie opportune e deve attingere a piene mani al know-how che posseggono i produttori delle macchine, gli utilizzatori delle stesse e i fornitori». In tal senso, spiega Prete, SKF ha creato programmi strutturati volti al miglioramento delle performance dell’impianto e dei processi produttivi in generale. La modalità di intervento si esplica in tre step: effettuare un’analisi delle esigenze delle aziende e misurarle, studiare soluzioni apposite, impostare una manutenzione strutturata.
I primi elementi da considerare quando si punta all’efficientamento di un processo produttivo sono gli asset, ovvero gli impianti.
Nella valutazione di dove e come intervenire vanno analizzati tutti gli elementi che intervengono nel ciclo di vita di un macchinario: «si guarda alla gestione e alla lubrificazione, a come viene effettuata e a come può essere migliorata; si verifica se esista una diagnostica, se ci sia l’acquisizione del dato e se quel dato sia interpretato correttamente». Un aspetto quest’ultimo molto importante in quanto, grazie a tale interpretazione, possono essere fornite ai team di manutenzione le indicazioni per poter intervenire in maniera tempestiva. «Si guarda però anche ad altri elementi quali, per esempio, l’apporto dell’ingegneria delle applicazioni e degli uffici tecnici, e la capacità di reazione della supply chain». Ma si deve prendere in considerazione anche a un’altra possibilità, utilizzare un tipo di pratica che Prete definisce “virtuosa” e che punta al riutilizzo dei materiali: il ricondizionamento.
Rigenerare e ricondizionare
SKF, in questo ambito, ha implementato due nuovi programmi: ReconOil, per la rigenerazione degli oli industriali, e SKF Bearing ReMan, per il ricondizionamento dei cuscinetti (Figura 1).
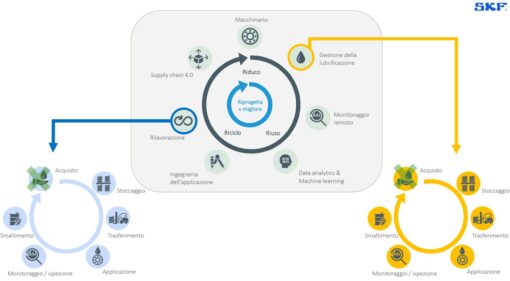
Il primo, afferma Prete, è un servizio che permette la rigenerazione dell’olio industriale. «Nell’utilizzo lineare dell’olio normalmente sono evidenti tre step» spiega. «L’olio usato in macchina è sottoposto innanzitutto a una certa degradazione che avviene per contaminazione oppure per ossidazione o, ancora, per il consumo degli additivi all’interno dell’olio stesso, che sono gli elementi che ne assicurano la funzionalità. In caso di degradazione ovviamente occorre intervenire con una sostituzione. Già in questa fase si verifica un impatto dal punto di vista economico, legato ai costi di approvvigionamento dell’olio, ma anche alla capacità produttiva del processo. Alla sostituzione segue la fase di smaltimento, per la quale, oltre all’impatto ambientale che si genera, l’azienda deve affrontare dei costi».
La soluzione proposta da SKF permette di eliminare tutte queste incombenze, rigenerando l’olio e dandogli quindi una nuova vita. La rigenerazione avviene attraverso un processo di filtraggio innovativo: RecondOil. Il processo è strutturato in tre fasi: la prima di miscelazione, la seconda di decantazione e l’ultima fase di separazione e filtrazione fine. «Il sistema interviene con un doppio concetto di filtrazione: meccanica e chimica. All’interno dell’olio usato viene aggiunto un booster ovvero una sostanza che crea aggregati di particolato e di prodotti di ossidazione, questi aggregati subiscono un fenomeno di coalescenza in cui si legano l’uno all’altro e creano una serie di piccole gocce che, per decantazione, vanno a fondo del serbatoio. Terminato questo processo di natura chimica, che è impostato in base alla viscosità dell’olio e al suo livello di contaminazione, inizia una filtrazione di natura meccanica. L’olio decantato è portato in un altro serbatoio a cui è aggiunta una polvere di cellulosa che viene omogeneizzata con l’olio. A questo punto l’olio viene fatto passare attraverso una superficie ricoperta da un foglio di carta sul quale, per effetto della polvere di cellulosa, si crea una sorta di letto filtrante. In questo modo anche i residui di booster o di particolato che non erano riusciti a decantare precedentemente riescono a essere eliminati».
In termini pratici significa ottenere vantaggi degni di nota, sia dal punto di vista della riduzione dei costi sia da quello dell’impatto ambientale. A tale proposito Prete riporta i dati di un’analisi di LCA condotta da un istituto indipendente di ricerca ambientale svedese: lo studio ha rilevato che utilizzare un litro di olio con un approccio lineare genera circa 3.800 kg di CO2 equivalente, l’utilizzo invece di questi sistemi riesce ad abbassare il livello di emissioni del 96% circa.
La soluzione in un Box
Tra le soluzioni di SKF, nelle realtà di processo come quella del settore cartario trova maggiore impiego RecondOil Box (Figura 2).
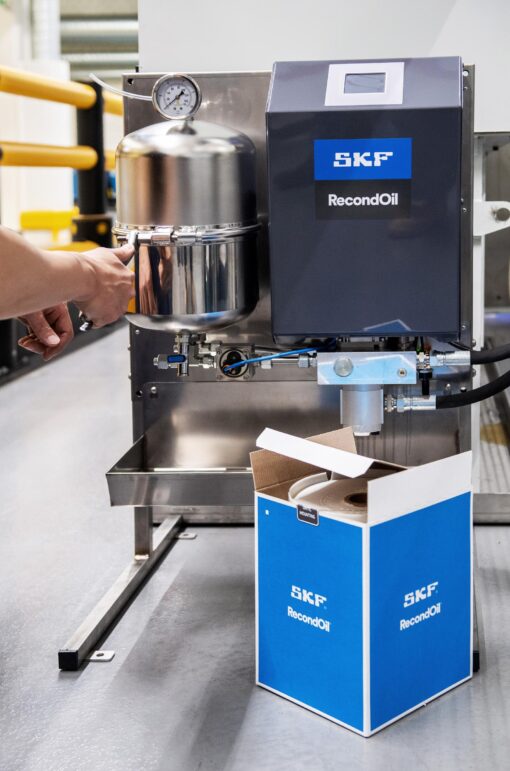
Si tratta di un sistema montato a bordo macchina che permette di eliminare dall’olio le microparticelle e le nanoparticelle (Figura 3).
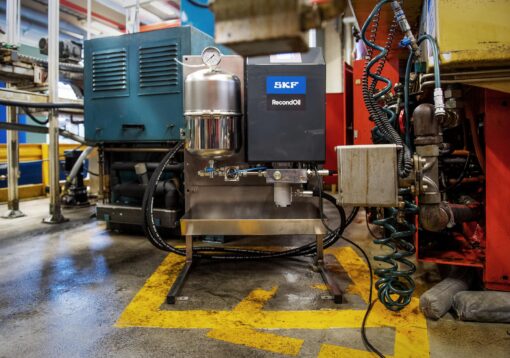
«Può dare grandi vantaggi, per esempio, nell’area delle seccherie in cui i cuscinetti dei cilindri sono lubrificati ad olio. La lubrificazione di un cuscinetto» spiega Prete « crea un velo di olio con uno spessore massimo di mezzo micron, che separa i corpi volventi e le piste. Avere quindi particelle di dimensioni macrometriche crea sfaldature e successive fratture dei cuscinetti. Mentre le nanoparticelle fungono da catalizzatore per l’ossidazione dell’olio, favorendola, per cui si genera un aumento della viscosità dell’olio e si formano lacche e sedimenti che possono ostruire i dotti di lubrificazione. Una condizione che può portare al guasto del cuscinetto e del sistema di lubrificazione. Avere un olio che è costantemente rigenerato dal sistema montato a bordo macchina permette, quindi, di avere una minore usura dei componenti» (Figura 4).
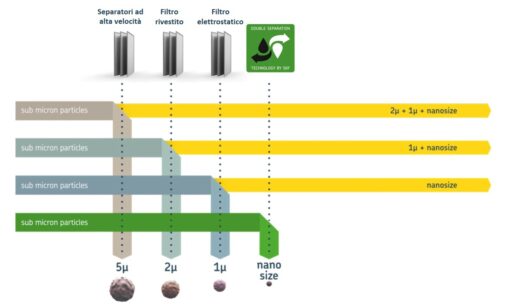
L’utilizzo circolare dell’olio – ovvero la sua rigenerazione – rispetto a un utilizzo lineare dunque comporta vantaggi in termini sia di costi operativi dell’impianto sia di impatto ambientale, con meno emissioni e meno smaltimento, e infine può generare un vantaggio sull’efficacia del processo produttivo (OEE, overall equipment effectiveness). Meno guasti significa avere anche meno fermi, meno interventi manutentivi e un incremento della vita utile dei componenti con una riduzione degli investimenti per l’acquisto di nuovi.
Ricondizionare i cuscinetti
Altro servizio offerto alle imprese è SKF Bearing ReMan, il ricondizionamento dei cuscinetti. Una pratica che permette di allungare la vita operativa del cuscinetto e di avere un rimando, ancora una volta, sui costi operativi. Un impatto, prosegue Prete, che sarà maggiore a seconda del tipo di cuscinetto con cui si avrà a che fare. «Se parliamo di un cuscinetto di dimensioni importanti per un monolucido piuttosto che per una shoe press, considerando che il prezzo di un ricondizionato è circa il 50 o 60% rispetto a quello di un cuscinetto nuovo, è chiaro quale sia l’impatto dal punto di vista dei costi operativi». Ma non è solo una questione di risparmio, «il ricondizionamento del cuscinetto è anche un valido strumento di indagine e di interpretazione delle eventuali anomalie di funzionamento della macchina. I carichi passano attraverso questi elementi quindi opriamo un’analisi dalle tracce di lavoro del cuscinetto e riusciamo a capire se ci sia qualche problematica di funzionamento del macchinario». Questo consente agli ingegneri di SKF di collaborare con i team di manutenzione delle imprese per risolvere poi tali problematiche.
Anche il ricondizionamento si sviluppa in più fasi: all’analisi, con un’ispezione visiva e verifica del magnetismo residuo, seguono una classificazione secondo la ISO 15243:2017 dei danneggiamenti che sono occorsi al cuscinetto e la redazione di un report che viene consegnato all’azienda cliente la quale deciderà, in base alle informazioni ricevute, se proseguire o meno con la pratica (Figura 5).
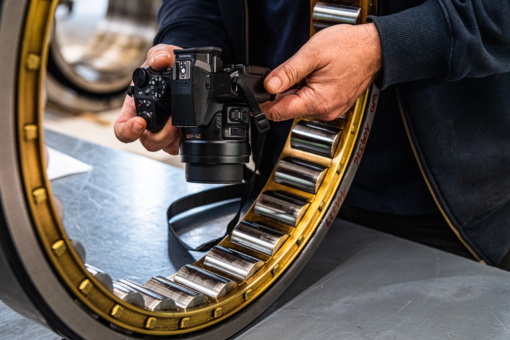
Se il cliente accetta si passa alla fase di ricondizionamento: ne esistono di diversi livelli in base alla necessità che alcuni componenti debbano essere rilavorati piuttosto che sostituiti (Figura 6).
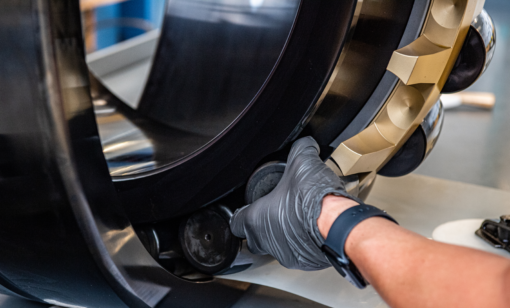
Terminato questo processo, il cuscinetto viene rimontato e misurato in tutte le sue componenti. In ultimo, ottiene una marcatura che gli consente di avere una tracciabilità unica, viene indicata la zona di carico potenzialmente migliore con la quale debba essere rimontato in macchina e viene effettuata un’ispezione finale a termine della quale viene redatto un certificato. Il documento garantisce il rigenerato come pienamente conforme a un cuscinetto nuovo e riporta la stima precisa e puntuale del risparmio in termini di emissioni che la pratica ha consentito di ottenere rispetto all’acquisto di un nuovo cuscinetto. Un elemento che, sottolinea Prete, può essere utilizzato dall’azienda cliente per dimostrare il proprio impegno nella riduzione delle emissioni indirette.
Anche il ricondizionamento, infine, ha un impatto ambientale notevole, «si stima che ricondizionare un cuscinetto porti a un risparmio in termini di emissioni di circa il 90%. Non solo, si è calcolato un utilizzo di energia che è tra il 60 e il 95% in meno rispetto alla produzione di uno nuovo cuscinetto, generando, oltretutto, anche una produzione inferiore di scarti». E Prete riporta un esempio concreto, «un cuscinetto che trova impiego, molto frequentemente, negli impianti di produzione della carta è il 230/630, dal quale ricondizionamento si riescono a risparmiare circa 957 kg di CO2».
Senza dubbio le sfide del settore manifatturiero sono tante, dice in ultimo l’ingegnere, «ciò che ci proponiamo di fare come SKF è di collaborare con le imprese nella definizione di una strategia manutentiva, dando indicazioni, condividendo il nostro know-how e fornendo soluzioni tecnologiche e pratiche virtuose».
Articolo tratto da Industria della carta, ottobre 2022