Insidiose perché, in determinate condizioni, possono incendiarsi e innescare esplosioni. Sono le polveri, un pericolo ancora oggi sottovalutato. Ma una corretta valutazione dei rischi e la scelta delle giuste soluzioni possono scongiurare danni a cose e a persone. Una società milanese si occupa proprio di questi sistemi di sicurezza.
Con diciassette anni di esperienza nel settore anti esplosione e una conoscenza approfondita di diversi processi industriali, Erigo è un’azienda esperta nella prevenzione e limitazione del rischio derivante dalla minaccia di esplosione da polveri.
Fondata nel 2000 da Paolo Chechi, che ne è amministratore delegato, Erigo è in grado di valutare e classificare i rischi nelle diverse situazioni, fornendo poi la soluzione tecnica più appropriata; il tutto nel pieno rispetto delle vigenti normative europee e nazionali in materia. Siamo andati a trovare gli esperti di questa società nella loro sede di Gorgonzola, a pochi chilometri da Milano, dove ci hanno raccontato di un mondo che, ancora troppo spesso, non si conosce a sufficienza.
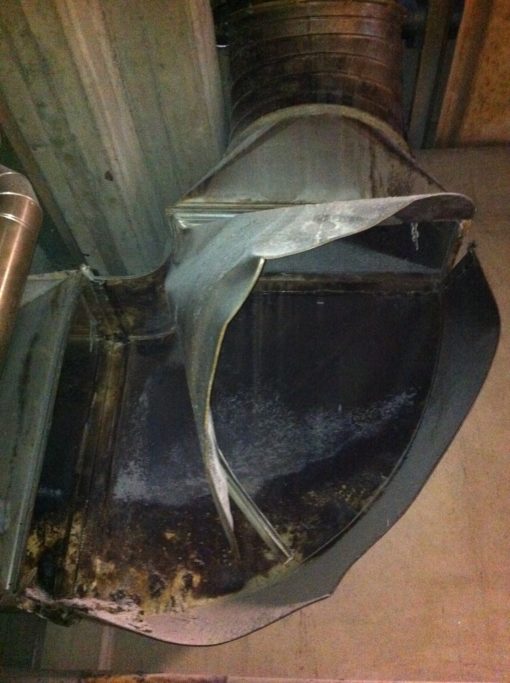
I comportamenti imprevedibili delle polveri sono alla base degli incidenti
Il tema delle polveri è critico e delicato quando si parla di cartiere, ma oggi sono disponibili soluzioni e accorgimenti tecnici in grado di mettere in sicurezza gli impianti e soprattutto chi ci lavora. Innanzitutto, ci spiega Chechi «un’esplosione è un’azione esotermica che genera un aumento di pressione e di temperatura»; i danni possono essere devastanti. L’esplosione di una macchina o di una parte di impianto non provoca solo danni alle cose, può generare anche incidenti molto gravi per le persone e il rilascio in atmosfera di sostanze nocive. Senza considerare poi il danno economico che comporta, in termini sia di danneggiamento vero e proprio sia di fermo produzione, anche per consentire le indagini giudiziarie, «non bisogna dimenticare infatti che anche il solo mancato adeguamento di un impianto costituisce reato. È vero che esistono le buone pratiche da poter seguire, ma possono accadere eventi imprevisti. Le statistiche su questa tipologia di incidenti ci dicono che il 20% delle cause resta da accertare». Il rischio, in pratica, va ben oltre ciò che ci si possa aspettare.
La pericolosità delle polveri, infatti, sta nel fatto di avere un comportamento poco prevedibile. Si possono accumulare in alcune parti dell’impianto, possono essere composte da miscele diverse e reagire in base a ciò che c’è nell’ambiente. I fattori di rischio sono numerosi e per innescare un’esplosione è sufficiente lo sfregamento tra le particelle. «Le peggiori conseguenze si hanno con la propagazione dell’esplosione che, passando in altri ambienti, può trovare nuovo alimento e generare così un effetto domino».
Nel settore cartario, per esempio, i punti più critici della linea di lavorazione sono i filtri di captazione della polvere e dei refili, la zona di taglio bobine e i punti di trasporto dell’amido. Un prodotto a rischio elevato, spiega Chechi, «basti considerare che è utilizzato come polvere test in quanto ha un coefficiente di esplosività ben preciso che corrisponde al limite massimo della prima classe di esplosività, immaginatevi quindi cosa significhi avere – come hanno le cartiere – un silo carico di amido».
Tecnologie e norme
La normativa di riferimento è la Atex – atmospheres explosibles – che raggruppa due differenti direttive europee: la 2014/34/UE, per la regolamentazione di apparecchiature destinate all’impiego in zone a rischio di esplosione – abrogativa della direttiva 94/9/CE – e la 99/92/CE per la sicurezza e la salute dei lavoratori esposti al rischio di atmosfere esplosive. L’Atex fu recepita dalla normativa italiana che la inserì prima nella Legge 626/1994, poi nel d.lgs 81/08 e, con il DM 3 agosto 2015, entrato in vigore il novembre successivo, rientra nel Testo Unico sulla prevenzione incendi.
«Evolvendoci anche noi insieme alla normativa» continua l’ad di Erigo «abbiamo iniziato a trattare tutti gli aspetti inerenti alla prevenzione e protezione da esplosioni: dalla classificazione delle aree, all’analisi dei rischi, con la compilazione del documento di valutazione dei rischi da esplosione, fino alla ingegnerizzazione dei sistemi di sicurezza contro incendi e rischi esplosione. Ci occupiamo inoltre di installazione e manutenzione dei sistemi, oltre che degli adeguamenti di apparecchi o parti di impianto secondo la formula chiavi in mano». L’azienda si rivolge alle imprese Oem, quindi a progettisti e costruttori di macchine, e all’utilizzatore finale. «In genere per l’industria cartaria lavoriamo con i costruttori, specializzati in particolare nella fornitura di sistemi di aspirazione e filtrazione».
Oltre al cartario però i settori interessati sono numerosi, in particolare quelli con movimentazione e stoccaggio di sfuso, quindi plastica, legno, carbone, acciaio, industria alimentare, agricola ecc.
Dai pannelli ai sistemi HRD
Nello specifico Erigo fornisce due tipi di sistemi di protezione: quelli passivi o meccanici, che reagiscono a un evento, e sono costituiti per esempio da pannelli che si rompono liberando in sicurezza l’esplosione o da valvole che si chiudono al momento opportuno evitando danni ulteriori; e quelli di tipo attivo, costituiti da sistemi a scarico rapido o soppressione come gli HRD – High rate discharge. Si tratta in ogni caso di sistemi normati; i pannelli di rottura e i pannelli per interno, dotati di arrestatori di fiamma, sono prodotti da Brilex, azienda tedesca, acquisita dal gruppo multinazionale austriaco Hoerbiger, uno dei maggiori produttori a livello europeo di questi prodotti. «In base ai dati forniti dal cliente e con l’ausilio di software specifici che stabiliscono accuratamente la superficie di sfogo, stiliamo i fogli di calcolo sui pannelli» spiega Chechi. Sono documenti obbligatori sulla cui stesura Erigo può fornire anche la dichiarazione di come siano stati effettuati. Mentre i sistemi HRD sono prodotti dall’azienda ceca Rsbp e sono dotati di sensori di pressione che hanno il compito di monitorare e misurare l’andamento della pressione ogni 0,5 millisecondi. «Se durante il monitoraggio per tre volte consecutive – quindi nell’arco di 1,5 millisecondi – il sensore rileva delle anomalie, viene inviato un segnale a una centrale del sistema che provvede a immettere nel circuito materiale in grado di sopprimere l’esplosione; in genere si tratta di fosfato di ammonio o bicarbonato di sodio». La quantità di materiale estinguente è rigorosamente misurata ed «è tale da riempire nel minore tempo possibile tutto il volume a disposizione. In questo modo si evita la possibilità di un’esplosione secondaria e l’apparecchio in cui è avvenuta l’esplosione viene immediatamente disaccoppiato dal resto dell’impianto e isolato per evitare un’eventuale propagazione dell’effetto».
Su richiesta Erigo è in grado anche di realizzare i test sull’esplosività delle polveri; «queste prove aiutano a comprendere esattamente con che tipo di sostanze si abbia a che fare nel caso specifico. Presso un’importante acciaieria, per esempio, stiamo effettuando otto diversi test sulle polveri che si formano durante i processi di lavorazione».
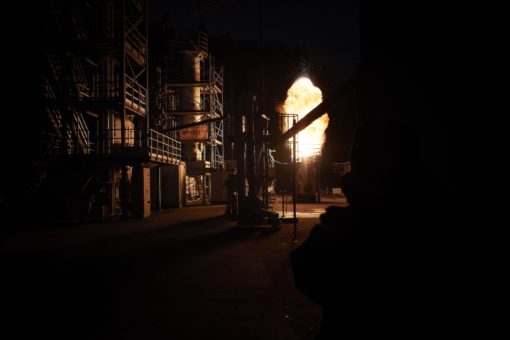
Dal progetto alla manutenzione
Partendo quindi dalla valutazione del rischio, fondamentale per capire quale sistema o strumento applicare, Erigo svolge e certifica l’installazione, in particolare di alcuni sistemi complessi come gli HRD. «Abbiamo personale specializzato, appositamente abilitato a installare ed effettuare controlli e manutenzione su questi impianti».
Si tratta sempre di progetti su misura, anche perché, come spiega Chechi, non c’è mai un impianto che possa essere uguale a un altro. Anche in caso lavorazioni simili, i fattori determinanti infatti sono sempre diversi: ambientali, legati all’uso della macchina, al tipo di produzione dell’azienda e al materiale che utilizza in linea. «Ci sono svariati parametri che continuano a cambiare e che si differenziano in base all’applicazione. Di volta in volta valutiamo quale sia la soluzione tecnologica più indicata». Si tratta pur sempre di un investimento per l’azienda, che si cerca però di razionalizzare minimizzando, dove possibile, i costi. «La cosa importante» sottolinea in ultimo Chechi «è che tutto sia in sicurezza».
«La sicurezza spesso è vista ancora come un obbligo e un costo, e si sottovaluta il pericolo determinato dalle polveri» Paolo Chechi, amministratore delegato di Erigo.